application scenario
In short-stroke, low-load applications, such as in some automated production lines, it is used to achieve simple material pushing, positioning, or clamping actions, such as part positioning and clamping during the assembly of electronic components.
Where safety is required, for example, in some pneumatic valves, when the gas source fails, the single-acting cylinder can automatically reset the valve to a safe position by means of spring force to ensure the safety of the system3.
Differences with double-acting cylinders
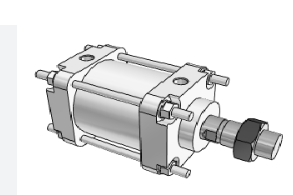
Working principle: The single-acting cylinder is pushed by one side air pressure, and the reset is by spring or external force; the double-acting cylinder is pushed by the alternating intake on both sides of the piston, which can move 467 in both directions.
Structural features: Single-acting cylinders are simple in structure, usually with one intake port and one exhaust port; double-acting cylinders are more complex, with two intake ports and two exhaust ports.
Thrust direction: Single-acting cylinders can only generate thrust in one direction; double-acting cylinders can generate thrust in two directions.
Control complexity: single-acting cylinder control is simple, control the gas supply and stop can be; double-acting cylinder control is relatively complex, requiring valves to control gas in and out to achieve two-way accurate movement.
Application range: Single-acting cylinders are suitable for simple linear push, such as door control and valve operation; double-acting cylinders are widely used in industrial and automation fields, such as pressure machinery, machine tools, etc.
Web: https://vpneumatic.com
Tex/Fax:0086-577-62840011
WhatsApp:0086-13355775769