When comparing the Oil-pressure Buffer and the Spring Damper, several key differences become evident in their working mechanisms, performance characteristics, and application scenarios.
Firstly, the Oil-pressure Buffer operates through the viscous damping effect of fluid flow. It converts part of the impact energy into heat and shock energy through gap throttle holes, providing a buffering function. Upon impact, the hydraulic oil flows through the discharge holes to mitigate the impact force, entering the oil storage chamber and compressing the reset spring. After the impact, the reset spring pushes the piston back, completing the buffer’s reset. In contrast, the Spring Damper relies on the characteristics of the spring to convert impact forces into elastic deformation energy, using the spring’s reaction force to decelerate the impact.
Secondly, in terms of performance, the Oil-pressure Buffer effectively eliminates spring fatigue, enabling friction-free operation. This enhances the equipment’s lifespan, reduces maintenance requirements, and minimizes operational noise. While the Spring Damper is cost-effective, it may suffer from increased rebound forces and speeds under excessive impact, potentially damaging equipment. Additionally, long-term use can lead to spring fatigue and noise generation.
Lastly, considering their applications, the Oil-pressure Buffer finds widespread use in various engineering machinery as a safety measure to prevent rigid collisions during operation. On the other hand, the Spring Damper, due to its unique characteristics and cost advantages, also finds application in specific areas.
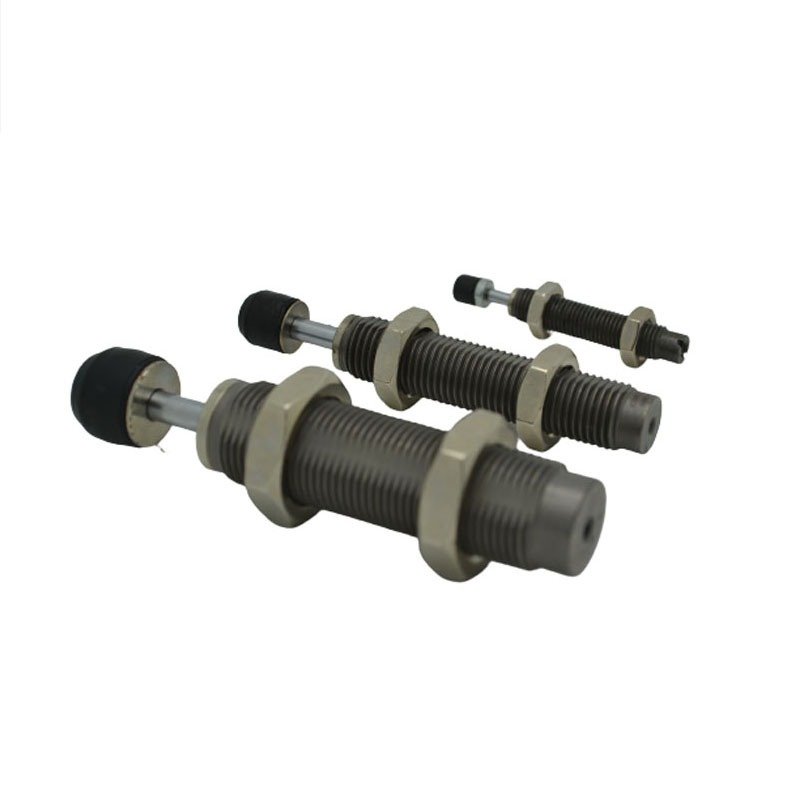
In conclusion, the Oil-pressure Buffer and the Spring Damper differ significantly in their working mechanisms, performance characteristics, and application scenarios. The choice between the two depends on specific application needs and scenarios.
Tex/Fax: 0086-577-62840011
WhatsApp: 0086-13355775769